Optimizing Fuel Efficiency in Shipping: Navigating External Influences
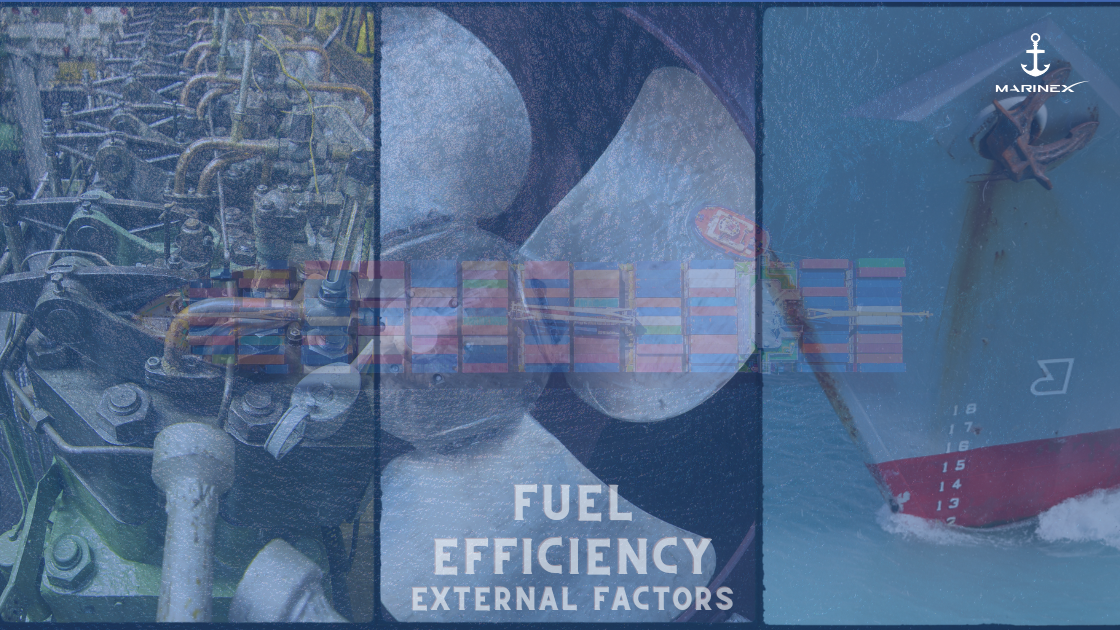
In the dynamic world of shipping, fuel consumption stands as a significant operational cost. Various external factors contribute to higher fuel oil consumption, presenting challenges for shipping companies seeking to balance cost-effectiveness with service quality. In this blog, we will explore the impact of four key external factors on fuel consumption and discuss strategies to control and optimize them.
Ship's Hull Condition
The condition of a ship's hull undeniably exerts a significant influence on fuel consumption. The movement of a ship is constrained by the resistance it encounters, characterized by two types: frictional resistance and residual resistance.
Frictional resistance is contingent upon the density of water, hull roughness, and the length of the ship. On the other hand, residual resistance stems from the wake-forming tendency induced by the ship's movement in water and its shape.
Hence, maintaining a clean hull is of paramount importance. Although various methods exist to clean the hull while the ship is afloat, the majority of these prove ineffective in the long run. Consequently, regular dry docking emerges as the optimal solution in ensuring the hull remains in optimal condition.
Any escalation in underwater hull roughness will amplify hull frictional resistance or vessel drag, resulting in an additional power requirement. This, in turn, leads to increased fuel consumption and higher costs associated with maintaining vessel speed.
Factors responsible for hull fouling encompass:
a) Use of improper techniques in applying paint.
b) Poor quality of applied paint.
c) Extended port stays or anchorage.
d) Damaged hull surface.
e) Inadequate maintenance of the hull protective system.
Addressing these factors is crucial to diminish the extent of hull fouling. The application of approved antifouling paint and a well-maintained antifouling system play pivotal roles in the ship's regular operating period between dry docks.
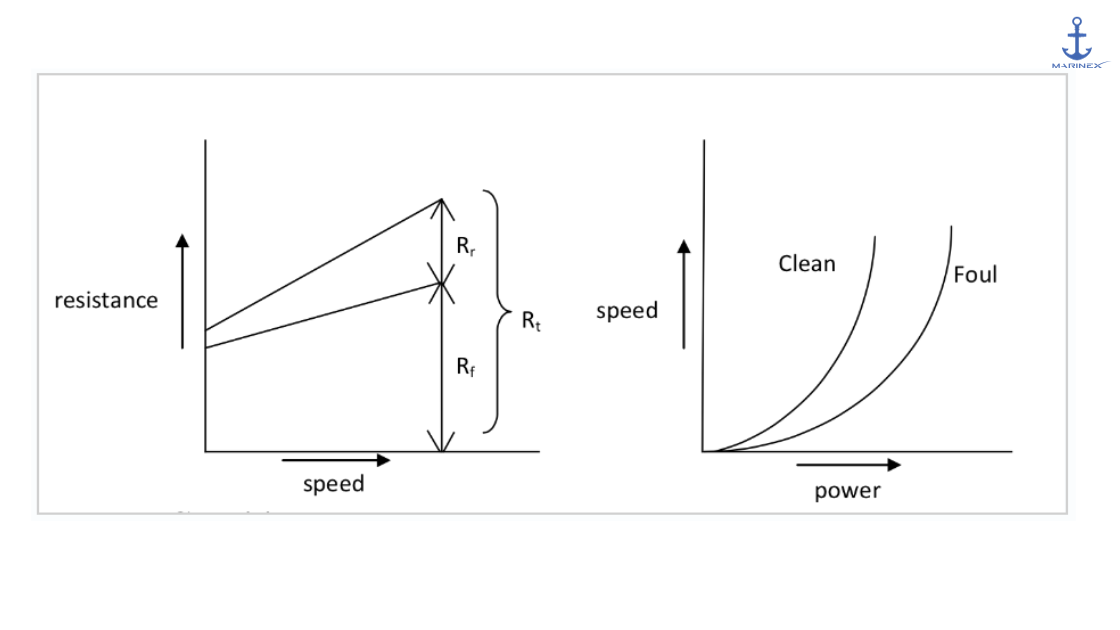
It is observed that the pattern of ship fouling is not consistently regular. As depicted in the speed/power graph, fouling may manifest as slow in initial stages or standardized in the early years, but over time, it becomes increasingly rigid or accelerated.
The speed and power graph also serves as an indicator that the engine may be subjected to thermal overload with a badly fouled hull, resulting in a shortened operating life for machinery parts, frequent breakdowns, and imposing substantial costs on shipping companies.
The application of approved antifouling paints and the maintenance of an efficient antifouling system are critical elements in ensuring the smooth operation of ships during their regular periods between dry docks.
Weather Conditions
Ships are meticulously designed and constructed to endure the forces of nature up to a specific threshold and for a defined duration. The ever-changing weather conditions and the state of the sea vary depending on the area of trade.
Extreme seasons like summer, winter, or intense monsoons are commonplace in the shipping industry. Favorable climatic conditions result in a positive slip, where the ship travels a greater distance than specified by the engine.
Conversely, adverse or severe weather conditions contribute to a negative slip, leading to extra fuel consumption due to heightened power demands and engine overloading.
Exercising good judgment and staying abreast of regular updates on weather conditions empower the ship's master to alter routes strategically, avoiding unfavorable weather conditions. This proactive approach can significantly reduce fuel consumption over the long run.
During severe weather conditions, adherence to engine manufacturer guidelines is imperative. Parameters such as governor load index, hunting, RPM, scavenging air limit, and torque limits must be meticulously considered to prevent thermal and mechanical overloading of the engine. Following these guidelines becomes instrumental in maintaining fuel consumption within acceptable limits.
Weather routing, involving the utilization of weather routing services, proves indispensable in avoiding rough seas and head currents. This strategic approach not only enhances safety but also optimizes voyage efficiency, contributing to prudent fuel management and operational effectiveness.
Maintenance of Different Elements in the Fuel Oil System
While the condition of the hull and weather significantly influence fuel consumption, the elements directly controlling fuel exhibit a proportional relationship to fuel usage.
When these components are well-maintained, substantial fuel savings can be achieved. Components such as fuel injectors, fuel pipes, fuel pumps, and the VIT RACK shock absorber, if subjected to regular inspection and proper overhaul, can minimize issues such as fuel leakages.
The various elements of the fuel oil system include:
- Fuel Oil Injector: It should be regularly changed/Overhauled following the manufacturer's guidelines after a fixed number of running hours. Overhauled and tested valves should be used.
- Fuel Pumps: Injector timings need regular checks and adjustments as required.
- VIT (Variable Injection Timing): Should be adjusted as per requirements. The VIT mechanism, fuel control rack, and their connection with the governor must undergo periodic lubrication to eliminate sluggishness and wear and tear.
- Fuel Oil Filter: Requires regular cleaning.
- Viscotherm: Regular maintenance and ensuring proper fuel oil temperature to achieve the desired viscosity, as per the fuel oil analysis report.
- Service Tanks: Proper temperatures should be maintained.
- Greasing of Fuel Linkage: Essential for smooth operation.
- Operation and Maintenance of Purifiers: Should always be carried out for proper operation.
Immediate attention to pipe joints, valve/vessel glands, booster pump section, or any fuel oil leakage in the fuel oil system also enhances the safety of the ship. Maintaining the proper temperature of fuel supplied to the engine is crucial for optimum efficiency.
Damage to Propeller Blades
Propellers must be maintained in top condition consistently, as several factors can detract from their optimum state, including fouling, cavitations, and physical damage. Any distortion from their true shape can lead to an imbalance, causing vibrations, increased cavitations, loss of thrust, drive shaft damage, wear on numerous bearings, and increased fuel consumption due to decreased efficiency.
- Propeller blades can sustain damage or roughness due to cavitation damage, calcium deposits, mechanical damage, and marine fouling. While the surface area of the propeller is small compared to the entire hull, the impact of a rough or damaged propeller on fuel consumption is substantial.
- Remedies for a rough propeller are economically viable, quick to execute, and represent a high return on investment compared to fixing a rough hull. Propellers can be cleaned or polished in water or during dry dock.
- Economically, the fuel savings from more frequent cleaning of a propeller outweigh the cleaning costs. This cleaning process can be economically combined with a general hull inspection by divers.
Physical damage primarily causes vibration, and the solution is to trim the blades equally to remove the damage and achieve a proper balance, reducing excessive cavitation. Careful trimming is essential to avoid exacerbating the problem.
Blade edge damage, such as cracks, bends, or breaks, may be repaired without removing the propeller from the shaft, depending on the extent of the damage. Slight distortions along the blade edge can usually be straightened cold by careful hammering. However, a dye-penetrant examination should follow any straightening to identify cracks that may have resulted from the process.
DEFORMATION
Minor edge deformation can be corrected in situ using hand-operated straightening levers and a 'soft' flame heating torch (not oxy-fuel). Major straightening and pitch checking would be carried out in a shore-based facility.
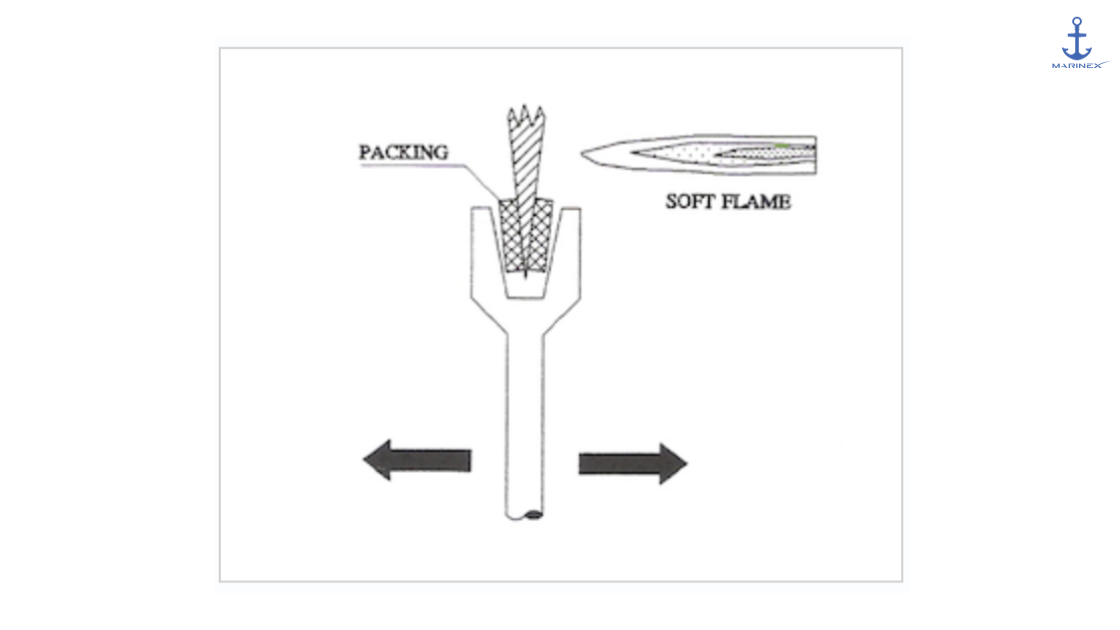
ROUGHENING
Roughening may lead to rapid degradation. Very small pits (less than 1 mm) can be ground out and polished. Deeper pits can be repaired by welding, grinding, and polishing. Temporary repairs can be carried out using resin fillers.
EDGE CRACKS
Minor edge cracks can quickly become more serious, especially at the leading edge. If the cracks are less than 10 mm in length, they can be ground out, and the edge 'faired.' Larger cracks may need to be repaired by drilling a small hole at the root of the crack, gouging out, welding, grinding, and polishing (not in the inner third of the blade). Temporary arresting of propagation has been carried out by drilling a small hole at the root of the crack, plugging the hole, grinding, and polishing.
SERIOUS EDGE DAMAGE
Repaired by welding on a new cast piece of the blade. The blade is cropped, and the new portion is clamped in position, welded on one side, ground flush, clamps reversed, the other side gouged, welded, and ground. A final polish gives the required finish to the blade surface.
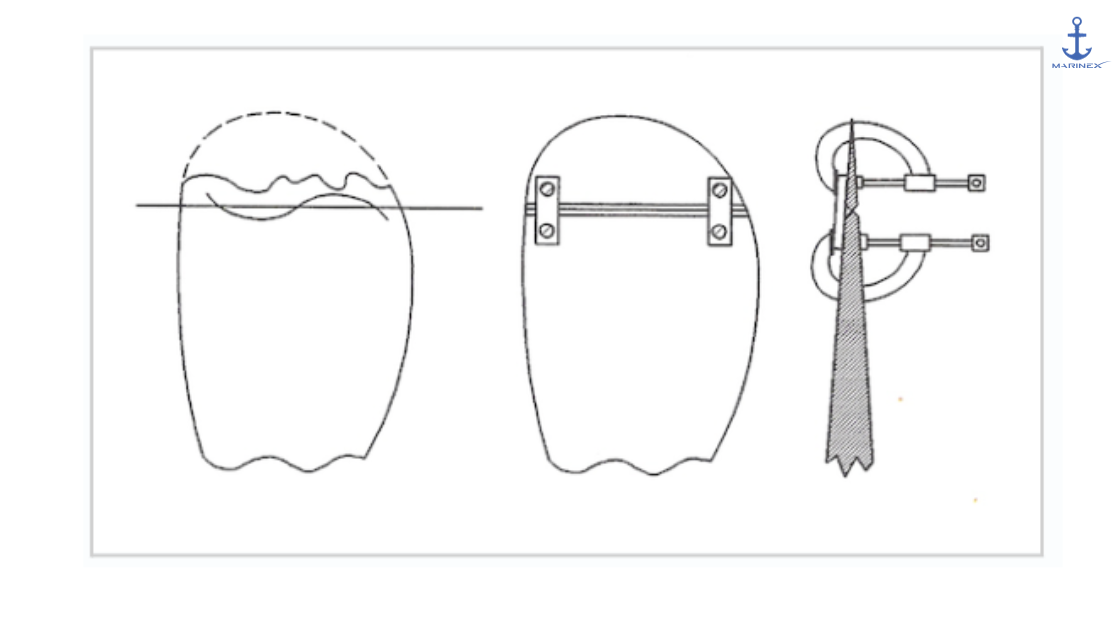
APPLICATION OF HEAT
This can be used to assist the fitting/removal of some propellers, but great care must be taken to avoid high residual stresses being introduced when cooling. The consequences of residual stresses could be 'stress corrosion cracking' of the boss, which may not occur until some weeks or months after the application of the heat. Stress corrosion cracking in the boss due to the incorrect use of heat for fitting/removal usually results in a scrapped propeller.
The heating process has been successfully carried out using steam, an electric blanket, or a soft flame produced by paraffin, propane, and air. A force flame, such as oxygen and fuel, should not be used. Under no circumstances should heat be used with shrink-fit bosses since the resin bond to the insert is destroyed.
There are three types of modification:
- Diameter Reduction: Easily and inexpensively performed underwater, this is the usual method for increasing RPM and balancing the ratio. The blade tips are cropped and faired.
- Pitch Reduction: This involves the twisting of blades and can only be accurately done in a workshop as blades need to be heated to prevent cracking. Although more expensive, this is the most effective modification as there is no loss of blade material. It is ideally suited to blades smaller than 4,000 mm in diameter.
- Trailing Edge Modification: This is achieved by either bending the trailing edges or by cutting them. Both operations can be performed in water and can achieve an effect on the RPM of approximately 5%.
In conclusion, mitigating the impact of external factors on fuel consumption in shipping involves a comprehensive approach, from regular maintenance to informed decision-making based on weather conditions.
By implementing these strategies, shipping companies can achieve a balance between operational efficiency and cost-effectiveness in their fuel consumption.
A Free Quiz for all readers based on the blog. Click the button below or the quiz icon on the right-side tab to take a short quiz and test your knowledge.
Subscribe to MarineX premium plans to get full access to all features of this blog, such as MarineX Interactive Flashcards, Premium Quiz, and Additional Study Material