Fatigue Failure Explained: Causes, Mechanisms, and Recognition
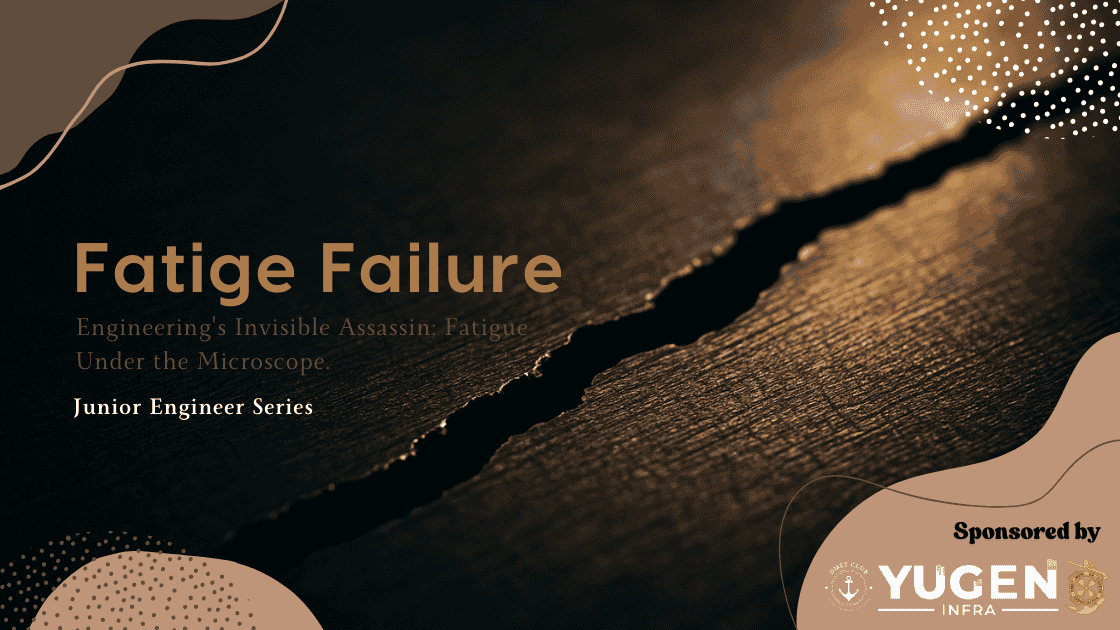
Fatigue failure is a critical concern in materials science and engineering, particularly for components subjected to cyclic or fluctuating stresses. Unlike static loading failures, fatigue failures can occur at stress levels significantly below a material's ultimate tensile strength, making them particularly insidious. This blog delves into the intricacies of fatigue failure, exploring its causes, mechanisms, recognition methods, and mitigation strategies.
Understanding Fatigue Failure
Fatigue failure refers to the progressive and localized structural damage that occurs when a material is subjected to cyclic loading. Over time, these repeated stresses can initiate cracks that propagate and eventually lead to catastrophic failure. This phenomenon is especially prevalent in materials exposed to fluctuating tensile stresses, such as those found in automotive, aerospace, and structural applications.
Causes of Fatigue Failure
Several factors contribute to the initiation and propagation of fatigue cracks:
- Improper Design: Designs that incorporate sharp corners, notches, or sudden changes in cross-sectional area can lead to stress concentrations, which are prime sites for crack initiation.
- Material Selection: Using materials that are not suited for the specific loading conditions can result in reduced fatigue life. For instance, materials with low fatigue strength or poor resistance to environmental factors may fail prematurely.
- Manufacturing Defects: Flaws introduced during manufacturing, such as inclusions, voids, or surface imperfections, can act as stress concentrators and initiate fatigue cracks.
- Improper Heat Treatment: Incorrect heat treatment processes can alter the microstructure of materials, affecting their mechanical properties and fatigue resistance.
- Surface Roughness: Rough surfaces can serve as initiation sites for cracks due to stress concentration at surface asperities.
- Environmental Factors: Exposure to corrosive environments can accelerate fatigue failure through mechanisms like corrosion fatigue.
Mechanism of Fatigue Failure
The fatigue failure process typically progresses through three stages:
- Crack Initiation: Micro-cracks form at points of stress concentration, often at the surface or near defects.
- Crack Propagation: With each loading cycle, the crack grows incrementally. The crack path is often perpendicular to the applied stress.
- Final Fracture: Once the crack reaches a critical size, the remaining cross-section cannot support the load, leading to sudden fracture.
During crack propagation, features known as "beach marks" or "striations" may appear on the fracture surface, indicating the incremental growth of the crack .
Recognition of Fatigue Failure
Identifying fatigue failure involves examining the fracture surface:
- Smooth Area: The region where the crack initiated and propagated slowly appears smooth and may show beach marks.
- Rough Area: The final fracture area, where rapid failure occurred, appears rougher and may exhibit a "cup and cone" morphology in ductile materials.
The presence of both smooth and rough regions on the fracture surface is indicative of fatigue failure.
Mitigation of Fatigue Failure
To reduce the risk of fatigue failure:
- Design Optimisation: Avoid sharp corners and sudden changes in cross-section. Use fillets to reduce stress concentrations.
- Material Selection: Choose materials with high fatigue strength and suitable for the operating environment.
- Surface Treatments: Processes like shot peening or surface hardening can improve fatigue resistance by inducing compressive residual stresses.
- Quality Control: Implement rigorous inspection procedures to detect manufacturing defects.
- Protective Coatings: Apply coatings to protect against environmental factors like corrosion.
Conclusion
Fatigue failure is a complex process influenced by design, material properties, manufacturing quality, and environmental conditions. Understanding the mechanisms and recognizing the signs of fatigue failure are crucial for preventing unexpected failures in engineering components.
References
- Fatigue (Material) - Inspectioneering
- Fatigue (material) - Wikipedia Wikipedia
- Fatigue Failure - ScienceDirect Topics Fractory+5ScienceDirect+5ScienceDirect+5
- Understanding the Anatomy of Fatigue Failure - Interface Interface
- Fatigue & Overload: Part II, 4 Mechanisms of Component Failure - Reliability.com
- Fractography - Wikipedia Metallurgical Failure Analysis+4Wikipedia+4SlideServe+4
Illustrative Images Sources From Web
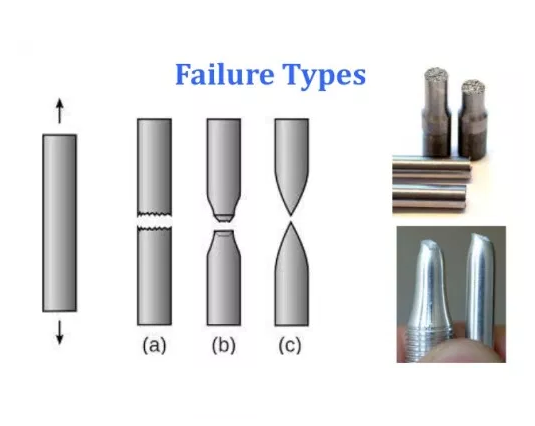
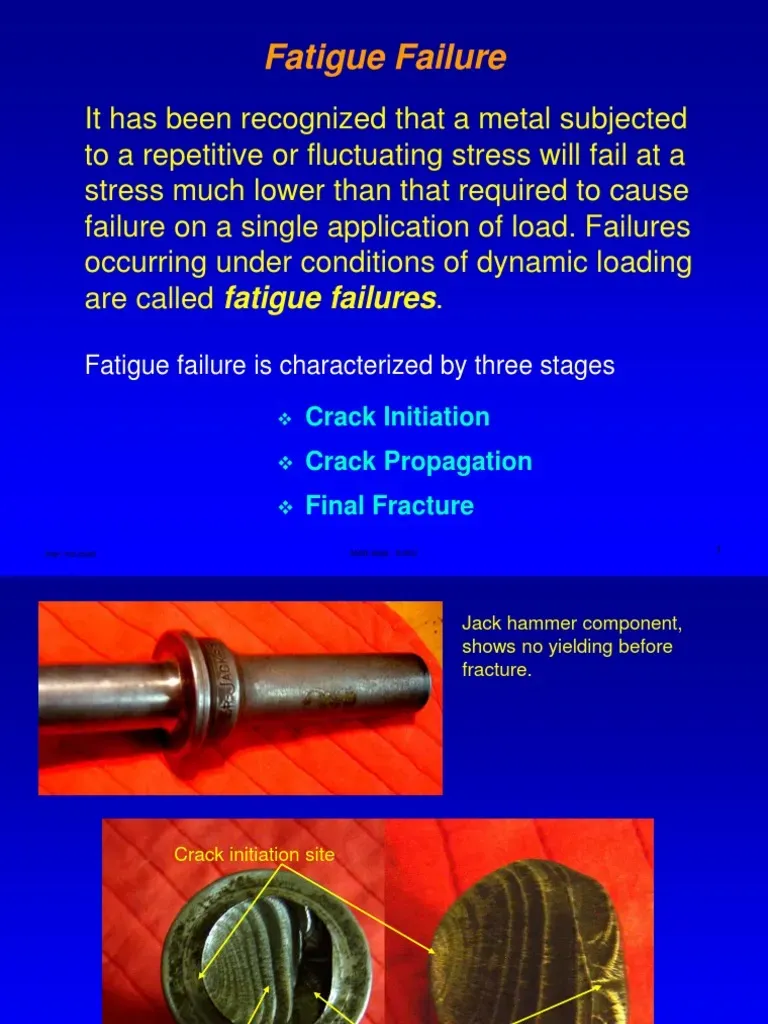
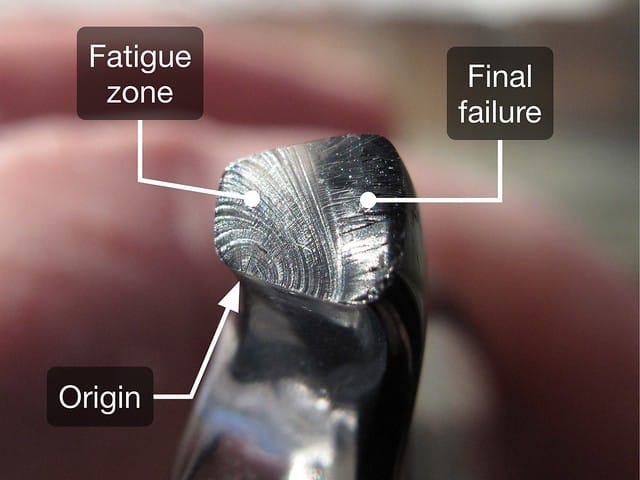
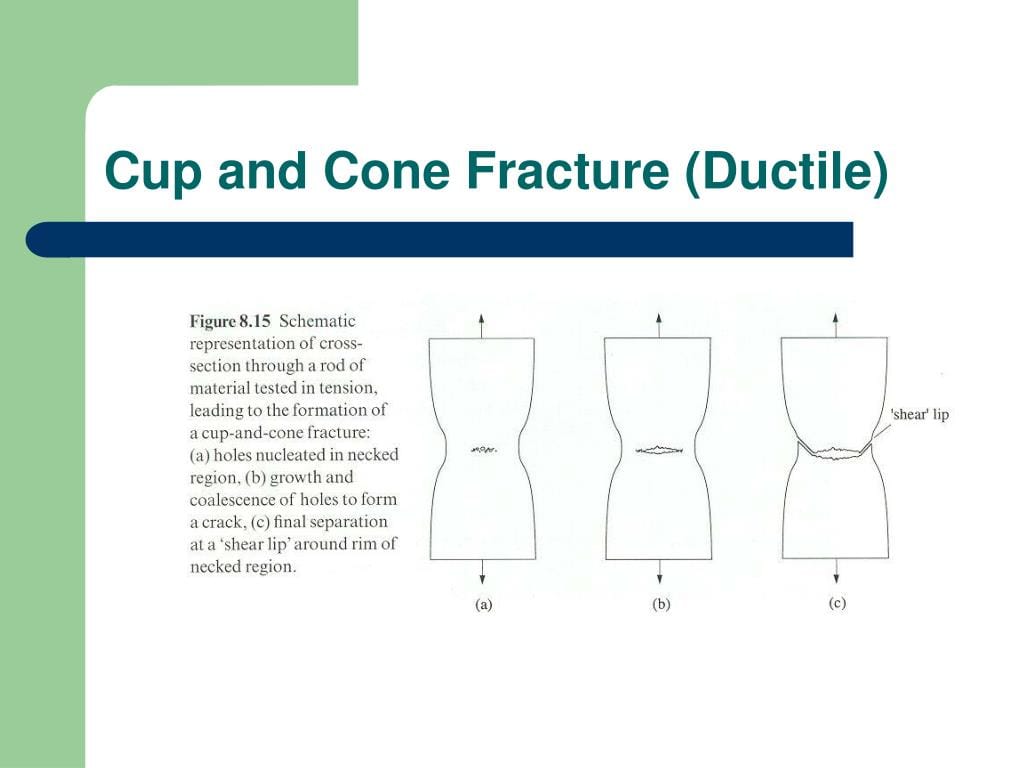
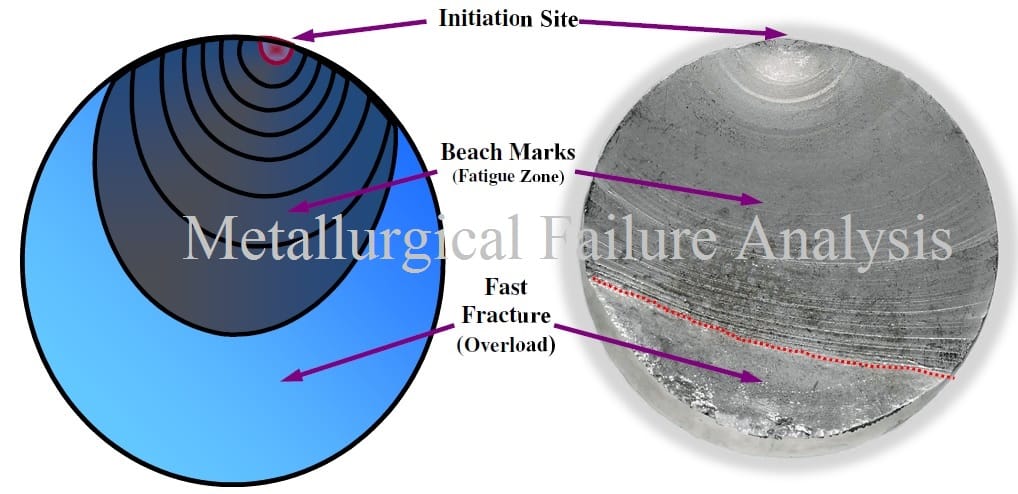
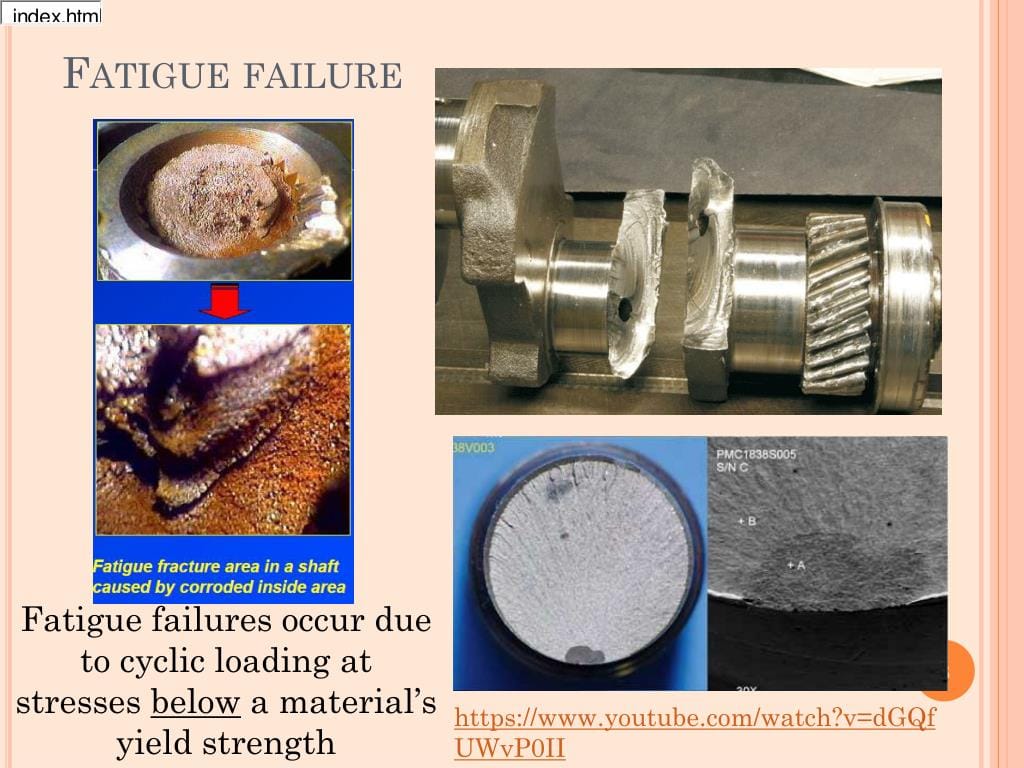
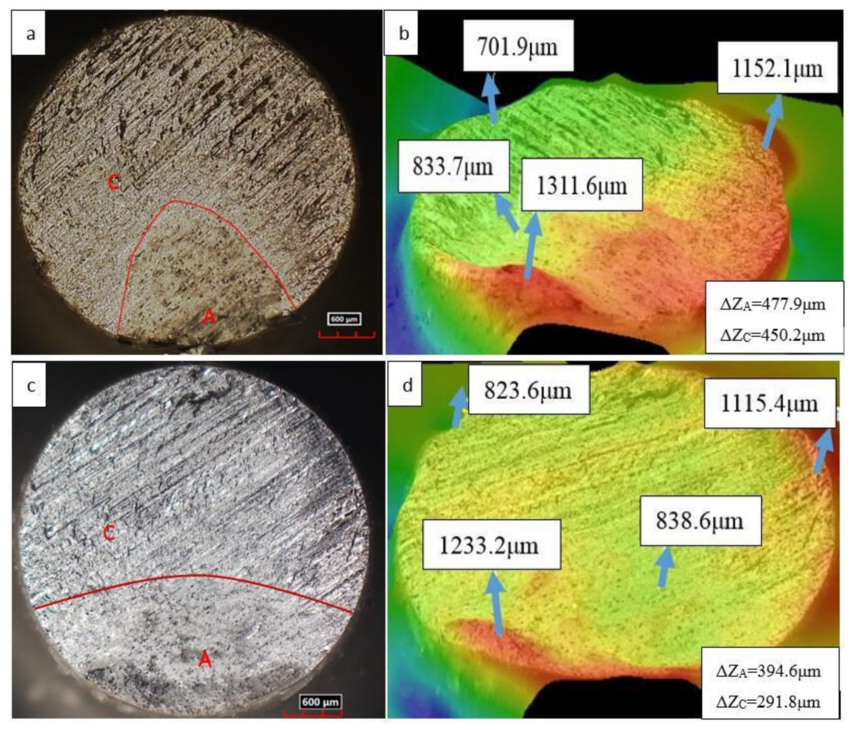
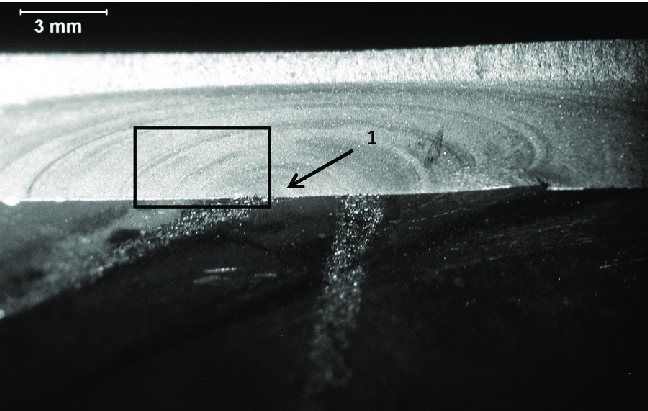
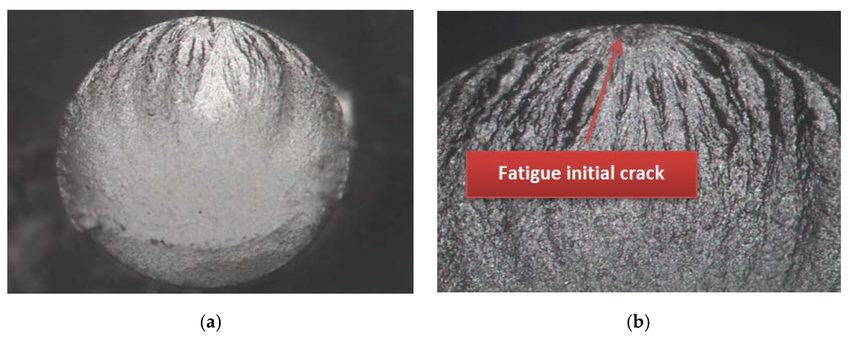
Sponsored Advert
📚 Practical Advice for Marine Engineers: Dealing with Fatigue Failure Onboard
Fatigue failure is one of the silent enemies of machinery and structural integrity on ships. It often starts invisibly but can lead to catastrophic failures if not detected and addressed early. For marine engineers working in challenging and isolated environments at sea, awareness and preventive practices are critical.
Here’s a structured guide:
1. Understand the Risk Zones
🔹 Critical Components: Pay close attention to components subject to fluctuating stresses — such as propeller shafts, crankshafts, connecting rods, rudder stocks, deck fittings, hydraulic cylinders, and cargo gear.
🔹 Stress Concentration Points: Watch areas around notches, weld joints, bolt holes, and sudden cross-sectional changes.
🔹 Corrosion-Prone Areas: Fatigue is accelerated when components are exposed to seawater, oil mist, or humid environments.
2. Routine Inspection and Monitoring
🔍 Visual Inspections:
- Regularly inspect machinery for early signs of cracks, discoloration, or pitting.
- Use good lighting and magnifying glasses if necessary for small components.
🔍 Nondestructive Testing (NDT):
- Schedule periodic ultrasonic, magnetic particle, or dye penetrant testing especially for critical rotating and load-bearing parts.
🔍 Vibration and Noise Monitoring:
- Unusual sounds or vibrations can indicate crack initiation. Promptly investigate any anomalies.
3. Follow Proper Maintenance Practices
⚙️ Lubrication:
- Ensure that moving parts are adequately lubricated to reduce friction-induced fatigue.
⚙️ Tightening Torque:
- Always apply bolts and fasteners with correct torque values. Over-tightening or under-tightening can lead to localized stress concentration.
⚙️ Surface Finish:
- Maintain smooth surfaces during repairs. Rough surfaces accelerate fatigue crack initiation.
⚙️ Avoid Improper Welding:
- Poor welding practices create residual stresses and stress raisers. Certified welders must handle critical repairs.
4. Manage Operating Conditions Wisely
⚡ Avoid Overloading:
- Do not operate machinery consistently at maximum rated loads. Try to stay within the safe operational envelope.
⚡ Control Start-Stop Cycles:
- Excessive start-stop operations can induce fatigue in engines and rotating machinery.
- Use auxiliary systems efficiently to minimize frequent cycling.
⚡ Monitor Alignment:
- Misalignment in shafting systems can cause fluctuating loads leading to fatigue failure.